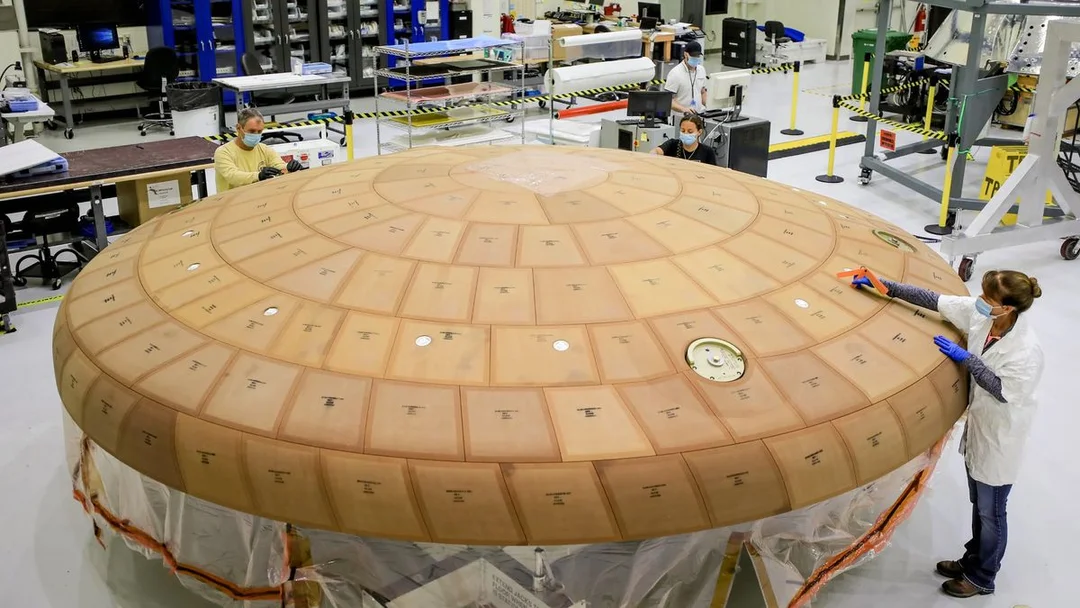
‘Sweating’ Spacecraft: The Future of Reusable Re-entry Heat Shields?
Imagine a future where spacecraft, upon returning to Earth, don't require extensive repairs or single-use heat shields. A team at Texas A&M University, in collaboration with Canopy Aerospace, is working to make this a reality by developing spacecraft that "sweat" – an innovative approach to keep reusable spacecraft cool during re-entry.
The current methods for protecting spacecraft during re-entry involve either ablative heat shields that burn away or heat-resistant ceramic tiles that require replacement. Both are costly and time-consuming.
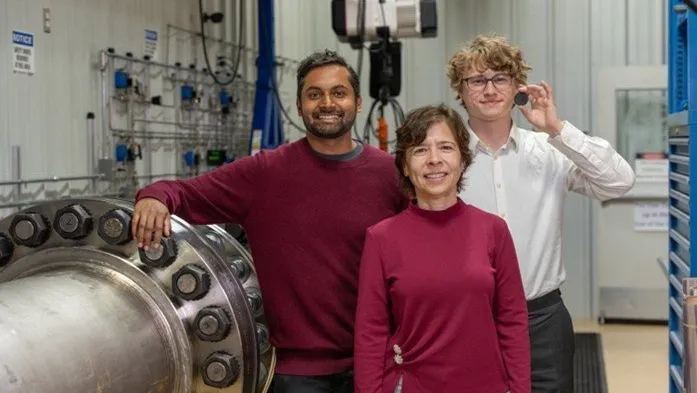
The team is developing a 3D-printed silicon carbide material designed to be both strong enough to withstand extreme atmospheric pressures and porous enough for a coolant gas to "sweat" through. This process, known as transpiration cooling, releases a layer of gas along the spacecraft's surface. This gas acts as an insulator, preventing direct contact with the intense heat generated by friction and compression of atmospheric gases during re-entry.
"Gas has a very low thermal conductivity," explained Hassan Saad Ifti, assistant professor of aerospace engineering. "This is why a puffer jacket is so effective. It traps air in these pockets, so it is the insulation from the air keeping you warm, not the solid part of the jacket."
Prototypes are currently undergoing testing to assess their ability to “sweat” and effectively insulate the spacecraft. William Matthews, a Ph.D. student leading the testing, stated, "We should see that the material's surface is cooler at hypersonic speeds when the coolant flow is introduced than the baseline when no coolant is present."
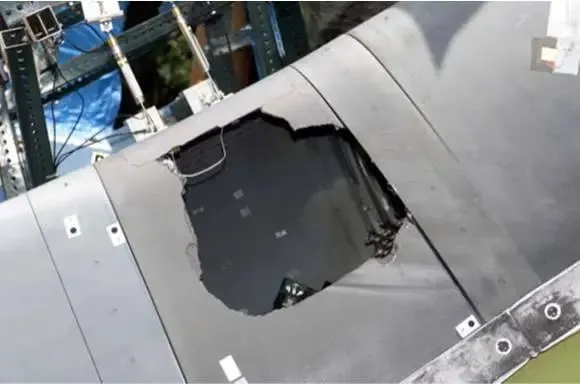
The concept of using gas as a protective layer isn't entirely new, but advancements in materials and testing are making it more viable. The Space Shuttle Columbia disaster in 2003, caused by damage to insulating tiles, underscores the critical need for robust heat shields. Transpiration cooling offers potential for quicker vehicle turnaround times, bringing them closer to the efficiency of a passenger jet.
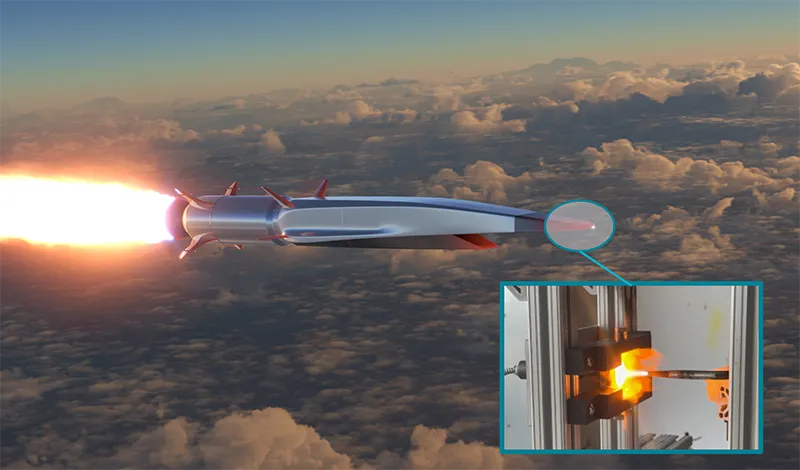
This research is supported by a $1.7 million Air Force Small Business Technology Transfer grant. Dr. Ivett Leyva, department head of aerospace engineering, emphasizes the importance of combining materials science and high-speed testing to ensure the project's success. "We are in a great position to bring together expertise on aerodynamics and high-speed testing to ensure this project succeeds," she said.
Could “sweating” spacecraft be the key to unlocking more affordable and frequent space travel? What other innovations could further revolutionize spacecraft reusability?
Leave your thoughts and comments below!